Unlocking Performance: The Critical Role of Engine Valves in Industrial Equipment
2024-11-15
Unlocking Performance: The Critical Role of Engine Valves in Industrial Equipment
Table of Contents
- Introduction to Engine Valves in Industrial Equipment
- Types of Engine Valves Used in Industrial Applications
- Functionality of Engine Valves and Their Importance
- Optimizing Performance Through Engine Valve Selection
- Best Practices for Engine Valve Maintenance
- Common Engine Valve Issues and Troubleshooting Techniques
- Future Trends in Engine Valve Technology
- Conclusion
- Frequently Asked Questions (FAQs)
Introduction to Engine Valves in Industrial Equipment
In the world of industrial machinery, performance hinges on various components working seamlessly together. Among these, **engine valves** play a pivotal role, influencing everything from efficiency to emissions. Engine valves are critical for regulating the flow of air and fuel into combustion chambers and the expulsion of exhaust gases. Understanding their function and maintaining them properly is essential for maximizing operational efficiency.
Types of Engine Valves Used in Industrial Applications
1. Poppet Valves
Poppet valves are among the most common types used in industrial engines. They feature a circular disc that opens and closes against a seat, controlled by a camshaft. Their design allows for precise control over the air-fuel mixture and exhaust flow, making them ideal for high-performance applications.
2. Butterfly Valves
Butterfly valves are primarily employed in applications where a quick shut-off is required. They consist of a rotating disc that allows or blocks flow. Although not typically used in combustion engines, they are crucial in controlling fluid flows in various industrial systems.
3. Gate Valves
Gate valves are designed for on/off control and are frequently used in pipelines. They provide minimal flow resistance when fully open, making them suitable for applications where quick or frequent operation is not required.
4. Check Valves
Check valves are used to prevent backflow in piping systems. They automatically close when the fluid attempts to flow in the reverse direction, ensuring the proper operation of various industrial processes.
Functionality of Engine Valves and Their Importance
Engine valves serve multiple functions that are crucial for the proper operation of industrial engines.
1. Air Intake Regulation
One of the primary roles of engine valves is to regulate the air intake into the combustion chamber. This regulation is essential for maintaining the optimal air-fuel ratio, which directly impacts engine performance and fuel efficiency.
2. Exhaust Flow Management
After combustion, the exhaust gases must be expelled efficiently to maintain engine performance. Engine valves facilitate this process, ensuring that exhaust gases do not linger and cause back pressure, which can lead to decreased efficiency.
3. Temperature Control
By regulating the flow of air and exhaust gases, engine valves also contribute to maintaining optimal operating temperatures within the engine. Overheating can lead to significant damage, making the functionality of these valves critical.
Optimizing Performance Through Engine Valve Selection
Selecting the right engine valves can significantly enhance the performance of industrial equipment.
1. Material Considerations
Choosing the right material for engine valves is crucial. Options include stainless steel, titanium, and other alloys that offer durability and resistance to heat and corrosion. The choice of material can affect the longevity and performance of the valves.
2. Valve Design and Configuration
The design and configuration of valves, including their size and shape, can influence airflow and exhaust efficiency. A well-designed valve will maximize airflow while minimizing turbulence, which is essential for maintaining high performance.
3. Compatibility with Engine Type
Different engines have unique requirements based on their design and intended application. Ensuring that the selected valves are compatible with the engine type can prevent issues and enhance overall performance.
Best Practices for Engine Valve Maintenance
Maintaining engine valves is essential for the longevity and efficiency of industrial equipment.
1. Regular Inspections
Conducting regular inspections of engine valves can help identify wear and tear early. This proactive approach allows for timely repairs or replacements, preventing larger issues down the line.
2. Proper Lubrication
Applying the correct lubricant ensures smooth operation of the engine valves and reduces friction. It is essential to follow the manufacturer’s recommendations regarding lubrication intervals and types.
3. Cleanliness of Components
Keeping engine valves and surrounding areas free from debris and contaminants is vital. Regular cleaning helps prevent clogging and ensures that valves operate efficiently.
Common Engine Valve Issues and Troubleshooting Techniques
Despite best efforts in maintenance, issues can arise with engine valves.
1. Valve Leakage
Leakage can occur when valves do not seal properly. This issue can lead to decreased engine performance. Troubleshooting involves checking valve seats for wear and ensuring proper alignment.
2. Sticking Valves
Valves can become stuck due to carbon buildup or inadequate lubrication. Regular cleaning and proper lubrication can prevent this problem. If sticking occurs, a thorough inspection is necessary.
3. Excessive Wear
Valves can wear out over time due to heat and pressure. Monitoring valve condition and replacing them at the first sign of significant wear is crucial to avoid engine damage.
Future Trends in Engine Valve Technology
As industrial equipment continues to evolve, so does the technology behind engine valves.
1. Advanced Materials
The development of new, lightweight, and heat-resistant materials is paving the way for more efficient engine valves. These materials can enhance performance and longevity.
2. Smart Valves
The integration of sensors and digital technology into valve systems allows for real-time monitoring and adjustment of valve operations, leading to enhanced efficiency and performance.
3. Environmental Considerations
With a growing focus on sustainability, future engine valve designs may prioritize reducing emissions and improving fuel efficiency, aligning with global environmental goals.
Conclusion
Engine valves are a cornerstone of efficient industrial equipment performance. By understanding their types, functionality, and importance, users can make informed decisions about valve selection and maintenance. Regular inspections, proper lubrication, and staying updated on technological advancements will further enhance the operational efficiency of industrial machinery. Investing in quality engine valves and adhering to best practices will ultimately lead to improved performance and longevity of equipment.
Frequently Asked Questions (FAQs)
1. What are engine valves used for in industrial equipment?
Engine valves regulate the flow of air and fuel into combustion chambers and control the exhaust flow, crucial for efficient engine operation.
2. How can I tell if my engine valves need maintenance?
Signs of valve issues include decreased engine performance, unusual noises, and visible leakage. Regular inspections can help identify problems early.
3. What materials are best for engine valves?
Stainless steel and titanium are popular choices for engine valves due to their durability and resistance to heat and corrosion.
4. How often should I inspect my engine valves?
Regular inspections should be conducted as part of routine maintenance, typically every few thousand operating hours or as recommended by the manufacturer.
5. What is the impact of valve design on engine performance?
The design of engine valves affects airflow and exhaust efficiency. Well-designed valves can significantly enhance engine performance by optimizing the air-fuel mixture.
Mobile Website
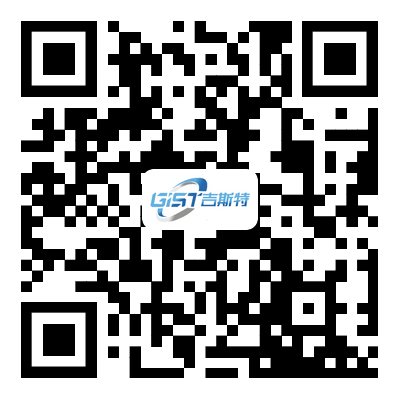
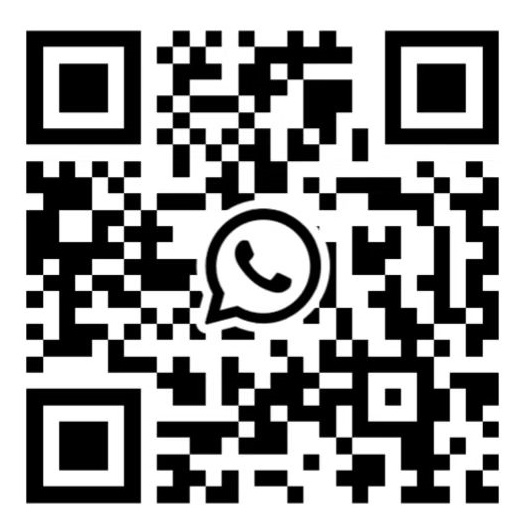
Hot Keywords
Total length cutting machine,
Rod end face grinding machine,
Lock clamping slot grinding machine, General grinding wheel taper grinding
language
English
العربية
বাংলাদেশ
Български
Hrvatski
Česky
Dansk
Nederland

Slovenski
Filipino
Suomi
Français
Maori

Georgian

Deutsch
Ελλάδα
ישראל
इंडिया
Magyarország
Ísland
Indonesia
Irlanda
Italia
日本語
Sovensko
Հայաստան
한국
Kyrgyz
ປະເທດລາວ

Latvian
Lithuanian
Luxembourgish

Macedonian
Малайская
Maltese
Монгол улс

ဗမာ

नेपाल
Norge
ایران
Polska
Portugal
România
Российская
Србија

Србија

Bosanski
Slovenian
Беларус
España
Sverige
Точик
ประเทศไทย
Türk
Azərbaycan
Uzbek

Việt Nam