Understanding the Valve Production Line: Essential Insights for Electrical and Electronic Manufacturing
2024-11-13
The valve production line is a crucial aspect of the manufacturing process in the electrical and electronic industry. Valves are essential components used in various applications, including fluid control systems in electronics, automotive, and industrial machinery. Understanding how these production lines function can enhance operational efficiency and product quality.
A valve production line typically incorporates various stages, starting from raw material handling to the final assembly of the valves. At the initial stage, high-quality raw materials, such as metals or plastics, are sourced and prepared for processing. The selection of materials is vital, as it directly impacts the performance and durability of the final product.
Once the materials are ready, the production process involves several manufacturing techniques, such as machining, molding, and assembly. These techniques are chosen based on the design specifications of the valves being produced. For instance, precision machining is often employed to ensure tight tolerances and high-quality finishes, which are critical for the valves to function effectively under varying conditions.
Automation plays a significant role in modern valve production lines. Automated machinery and robotics can enhance speed and reduce human error, resulting in more efficient production cycles. This automation not only increases productivity but also allows for consistent quality control throughout the manufacturing process.
Quality assurance is another critical component of the valve production line. Manufacturers often implement rigorous testing protocols to ensure that each valve meets industry standards and customer requirements. This may involve pressure testing, leak testing, and performance evaluations to identify any potential issues before the valves reach the market.
Furthermore, the layout of the production line itself can influence efficiency. A well-designed workflow minimizes unnecessary movements and optimizes space, allowing for a smoother transition from one production phase to another. Manufacturers often use lean manufacturing principles to eliminate waste and improve overall productivity.
In conclusion, the valve production line is a complex system that requires careful consideration at every stage of the manufacturing process. By understanding the intricacies involved—from material selection to automation and quality assurance—companies can improve their production efficiency and product quality. As the demand for electronic devices continues to rise, optimizing valve production lines will be essential for staying competitive in the electrical and electronic manufacturing sector.
A valve production line typically incorporates various stages, starting from raw material handling to the final assembly of the valves. At the initial stage, high-quality raw materials, such as metals or plastics, are sourced and prepared for processing. The selection of materials is vital, as it directly impacts the performance and durability of the final product.
Once the materials are ready, the production process involves several manufacturing techniques, such as machining, molding, and assembly. These techniques are chosen based on the design specifications of the valves being produced. For instance, precision machining is often employed to ensure tight tolerances and high-quality finishes, which are critical for the valves to function effectively under varying conditions.
Automation plays a significant role in modern valve production lines. Automated machinery and robotics can enhance speed and reduce human error, resulting in more efficient production cycles. This automation not only increases productivity but also allows for consistent quality control throughout the manufacturing process.
Quality assurance is another critical component of the valve production line. Manufacturers often implement rigorous testing protocols to ensure that each valve meets industry standards and customer requirements. This may involve pressure testing, leak testing, and performance evaluations to identify any potential issues before the valves reach the market.
Furthermore, the layout of the production line itself can influence efficiency. A well-designed workflow minimizes unnecessary movements and optimizes space, allowing for a smoother transition from one production phase to another. Manufacturers often use lean manufacturing principles to eliminate waste and improve overall productivity.
In conclusion, the valve production line is a complex system that requires careful consideration at every stage of the manufacturing process. By understanding the intricacies involved—from material selection to automation and quality assurance—companies can improve their production efficiency and product quality. As the demand for electronic devices continues to rise, optimizing valve production lines will be essential for staying competitive in the electrical and electronic manufacturing sector.
Mobile Website
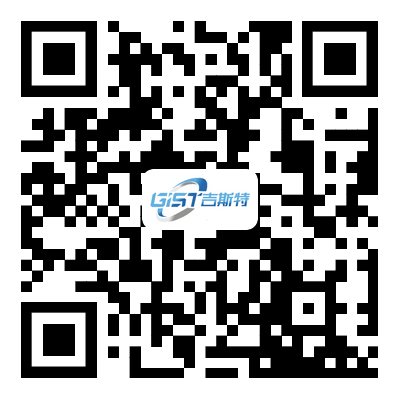
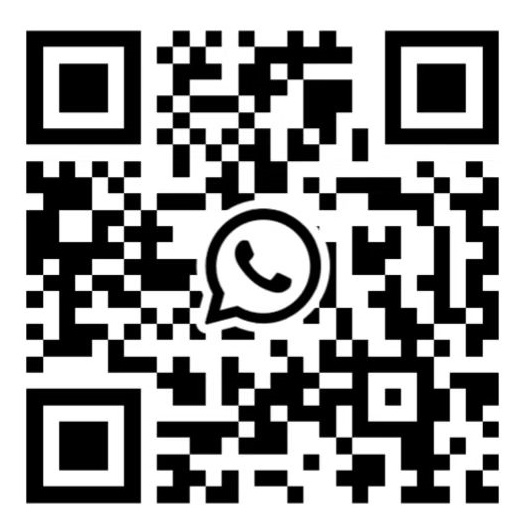
Hot Keywords
Total length cutting machine,
Rod end face grinding machine,
Lock clamping slot grinding machine, General grinding wheel taper grinding
language
English
العربية
বাংলাদেশ
Български
Hrvatski
Česky
Dansk
Nederland

Slovenski
Filipino
Suomi
Français
Maori

Georgian

Deutsch
Ελλάδα
ישראל
इंडिया
Magyarország
Ísland
Indonesia
Irlanda
Italia
日本語
Sovensko
Հայաստան
한국
Kyrgyz
ປະເທດລາວ

Latvian
Lithuanian
Luxembourgish

Macedonian
Малайская
Maltese
Монгол улс

ဗမာ

नेपाल
Norge
ایران
Polska
Portugal
România
Российская
Србија

Србија

Bosanski
Slovenian
Беларус
España
Sverige
Точик
ประเทศไทย
Türk
Azərbaycan
Uzbek

Việt Nam